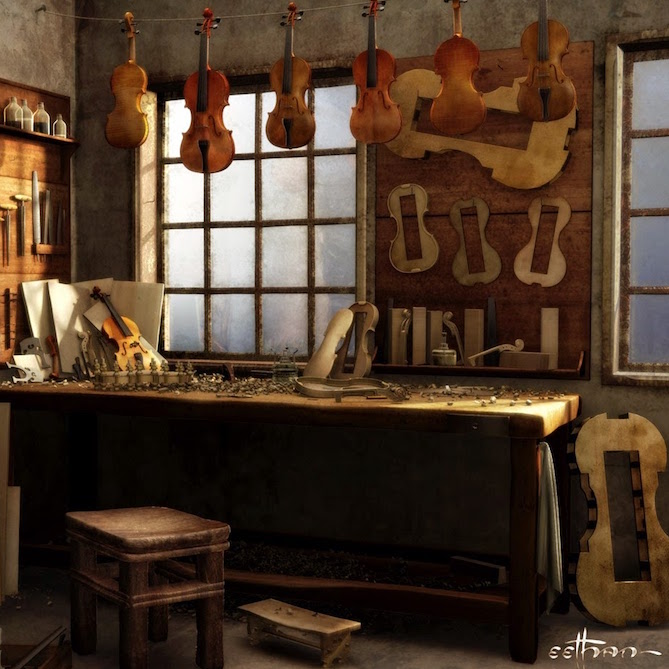
Know Your Cello
Wayne Burak
It’s far enough in the past that I can’t remember the exact day it happened. But I do remember the warning signs—the slightly racing pulse, the sweaty hands and labored breathing—you know, the need to pick up a woodworking plane, some files, chisels and fabricate a cello bridge.
I think I had been through several days of lectures on isorhythmic motet, compliments of Eastman music history, when one day my mind drifted into a world of cello parts, setups, fingerboards, tops, backs, ribs, and the most delectable feature – varnish. Really now, what is more enticing to look at than the iridescent play of colors jumping off of the cello back in the late afternoon sun in the Eastman Annex practice rooms? It’s simply enough right there to take you away from Dvorak, late Beethoven or even Piatti. So I was hooked. I knew it. Several thousand instruments later, 30 years have passed by.
So what has changed in the world of cellos?
What is there to know? Everything has changed and nothing has changed. Some of the old standby string brands are still being offered and remain unaltered. But, new advanced choices utilizing metals such as tungsten and hybrid stainless steel are everywhere. Some string models have been radically reformulated using software to plot resonance characteristics for various types of core materials. Torsional flex has become a topic backstage along with the ever present comparison of medium guages vs. forte or soloist. The addition of composite materials has altered our ideas about cellos, bows, cases, tailpieces, pegs, and endpins. Some of the new carbon graphite and synthetic materials offer lighter weight parts boasting improved resonance characteristics. And if that isn’t enough, there are literally dozens of rosin choices from every corner of the world. Yet, all of our cello life still passes through a ½ ounce handcarved maple bridge which has remained virtually unchanged in structure since before Bach wrote the cello suites! And, it still must be fitted by expert hands and trained eyes which through skill, intuition, and experience know just how to carve it for each cello’s most advantageous outcome.
Most of the cello world still relies on a classically handmade wooden cello with an ebony fingerboard, mixtures of various brands and types of setup parts, complimented by a bow constructed of a rare wood from Brazil – pernambuco. Hardly any of the basic parts of the classic acoustic cello structure have been significantly altered in the last 300 years except for the endpin, bass bar, neck angle, and corresponding higher bridge of different models. Speaking of performing, are you still using a chair while playing? We have recently witnessed cellists in contemporary settings moving around the stage sans chair. The cello then becomes a part of dance or a dynamic mobile voice not unlike the 17th century Italian processions where it was attached to the cellist by a front body harness for marching! ( I still personally advocate seated cello performances!)
OK, where does that leave us? I like to think of cello history and acoustical development as pieces of a dynamic evolving puzzle. It is a very good thing to have perspective on the past. If knowledge is power, lets first look at the physical aspects of what previous generations of enlightened luthiers and experts have left us and embrace these gifts and legacies. Along side of these timeless and priceless pieces of history fit instruments meeting the needs of current performance practice and trends. Pushing further into these new vistas, we see an intriguing world of contemporary handmade cellos, non-wood composite structures, acoustically amplified examples, electronic solid bodies, digitally processed, and midi instruments.
We will be exploring these topics and more in the coming weeks…
Subjects: Instrument Care
Tags: bows, Burak, cello bridge, cello setup, change, endpin, fingerboard, history, neck angle, pernambuco, plane, stage, strings, trends, varnish, Wayne, woodworking